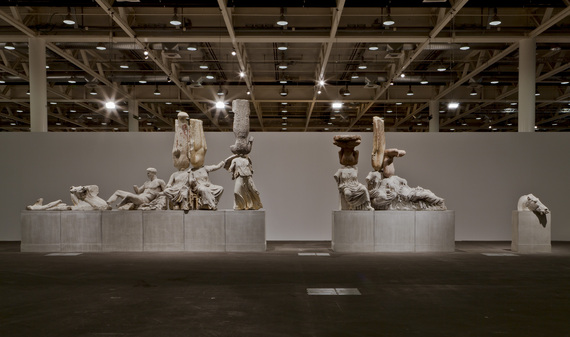
The entire field of sculpture--and its range of possibilities -- is undergoing an expansion and transformation. Digital technology, including 3-D scanning and CNC (computer numerical control) milling are facilitating and industrializing the creation of objects of extraordinary subtlety and complexity. "The use of 3-D modeling techniques changes the production time and the accuracy of the objects being produced," Xu Zhen explains, "but more importantly it also enables realizations of the imagination to a greater degree."
Mark Rossi, whose firm Handmade often works with sculptor Charles Ray, also has positive things to say about these developments: "3-D modeling enables the creation of objects (both virtual and subsequently physical) that cannot be created by other methods. It enables exploration and iteration more rapidly in some cases than model/pattern making can, and at potentially much lower cost. Also, shifts in scale can be accommodated immediately."
Xu Zhen, a conceptualist who describes himself as both an artist and curator, has the production of his works overseen by the MadeIn Company, which he founded and owns. According to Alexia Deheane of MadeIn, the process of making the final forms for Eternity began with 3-D scanning:
"First, we got permission to make scans of the original Parthenon sculptures. Their forms were initially scanned, worked on in 3-D software for more accurate detailing, and then printed in parts afterwards. Using the printed parts, we went back to traditional molding and casting, working with glass fiber reinforced concrete, sandstone, limestone, marble grains and mineral pigments. We worked with a team from Switzerland's Kunstgiesserei during the entire process."
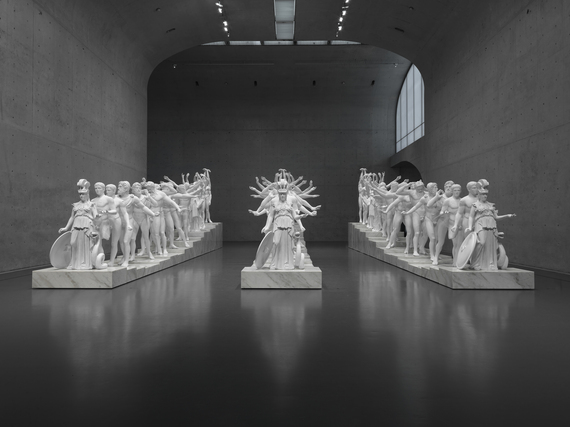
The reinforced concrete used in Xu Zhen's projects is only one many materials that is being utilized in conjunction with digitally based fabrication methods. Artificial stone composites, bound by cement or concrete, can be endowed with the appearance of natural stone through the addition of sand and crushed stone. Highly varied in terms of color, luster and weight artificial stone composites can be cast in a negative mold and then milled, chiseled, sanded and painted. Plaster, a familiar material often used in the 19th century for academic casts is also offering new possibilities. At Antiquity Stone in Morrisville, Pennsylvania, a dozen computer-operated stone cutting machines and two robots cut, mill and polish the works of owner/artist Jeff Koons, including his recent monumental plaster figure: Gazing Ball (Farnese Heracles).
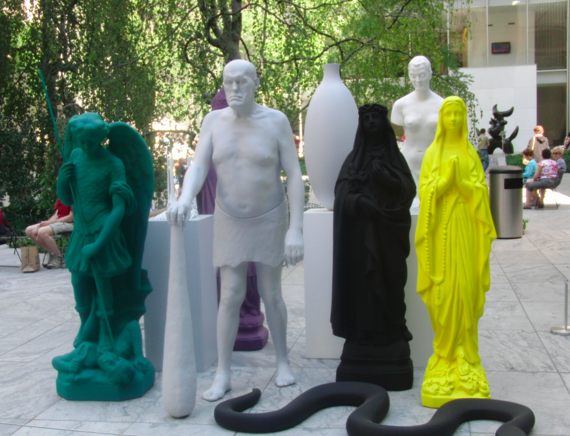
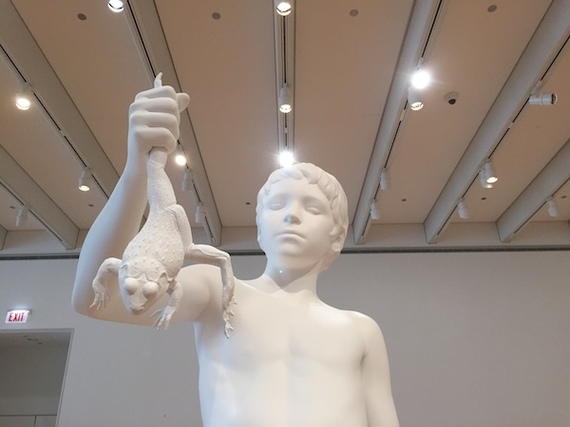
For artists who want to use new technologies and methods to realize their work, there are some notable problems to be faced. Mark Rossi of Handmade cites "high entry costs in initiating projects, size constraints on machine working envelopes and difficulty in working to create usable files for machining." Rossi thinks of high tech fabrication as "a tool in the box" and notes that it has "inherent restraints." Nonetheless, it is clear that technology is forever changing the range of sculptures formal and expressive possibilities.
Along with striking new possibilities, the rise of fabrication raises aesthetic questions. Among the questions raised is what digital modeling and production does to the "soul" of works of art but further distancing them from the physical touch of the sculptor and sense of "drawing" underlying the form. There is a tendency for forms based on 3-D models to look just a bit too perfect, like the imagery of a high-end digital animation. Some artists may want that effect, while others may find it cold.
Also, sculpture has always involved collaboration -- for example, between sculptors and foundries--but the trend seems to be that sculptors are more than ever generators of ideas who rely heavily on the skills and knowledge of collaborators to realize their forms. When the original sculptures of the Parthenon were made it involved the collaboration between quarrymen and carvers who engaged in intense physical toil. The making of works like those of Xu Zhen involve a great deal of effort of a different kind: software designers are the new quarrymen and industrial fabrication machines are the new carvers.